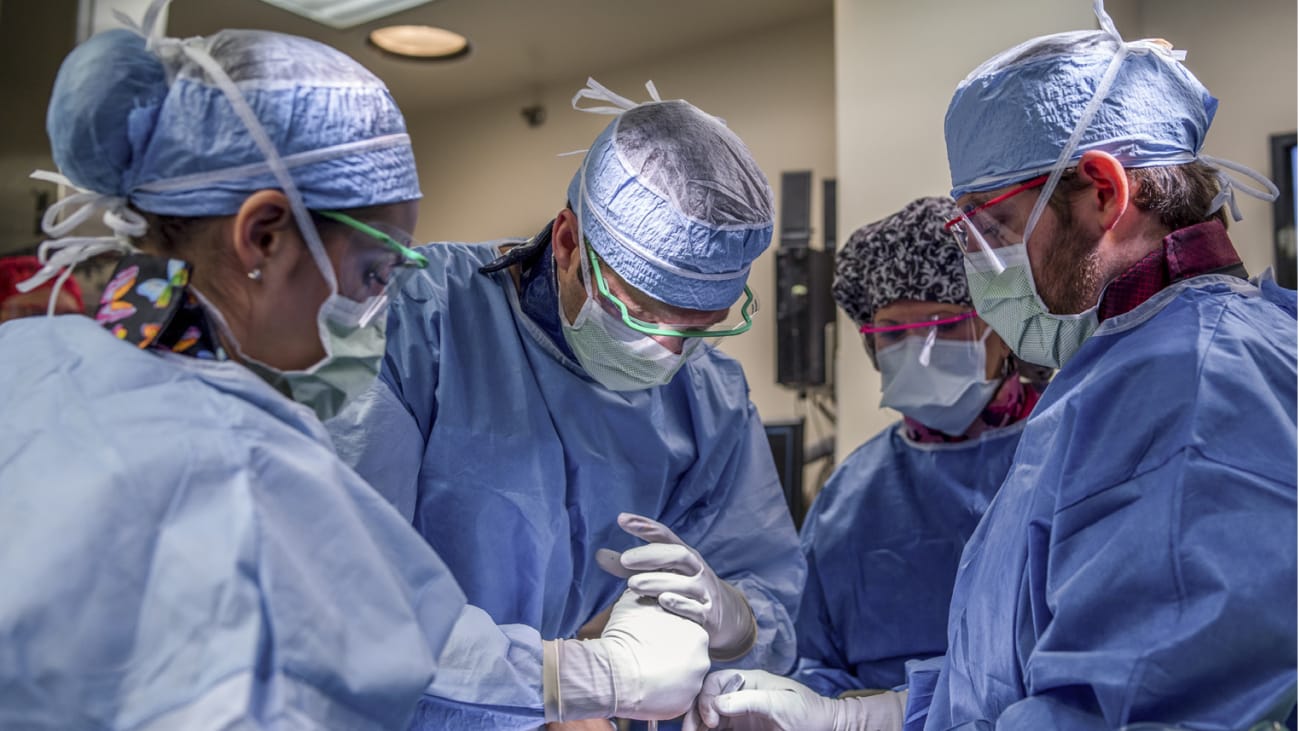
MUSC Health performs its first 3D-printed talus replacement
The talus connects the lower leg and foot and is crucial for foot and ankle mobility. But compared to other nearby bones — the tibia, fibula and calcaneus — it receives relatively low blood supply. For this reason, it takes a long time to heal.
Talus injuries are usually high-impact or trauma-related, such as a motor vehicle accident or fall. The bone can also be weakened non-traumatically, via long-term use of corticosteroids to fight autoimmune conditions. Regardless of whether it’s a traumatic or chronic injury, poor oxygenated blood flow may lead to the eventual death of the bone, known as osteonecrosis of the talus, or avascular necrosis (AVN).
AVN can be difficult to treat either conservatively or surgically. As Christopher E. Gross, M.D., an orthopedic surgeon at MUSC Health, explains, treatment choices until recently haven’t been optimal.
“Options range from core decompression, which is basically drilling a bunch of tiny holes into the bone to try to stimulate blood flow; to surgery to fuse the ankle and the entire hindfoot; to femoral allograft, in which bone and cartilage from a cadaver is placed into a damaged talus, along with a rod up the heel,” says Gross. Most surgical options, he explains, leave a patient with extremely limited mobility — like walking around in a ski boot for the rest of your life.
A new, exciting option
A recent patient of Dr. Gross’ is a 19-year-old woman, who had been taking steroids long-term due to lupus. A previous core decompression procedure had been unsuccessful, and she wanted to retain as much range of motion as possible. After reviewing all the options together, they decided to go ahead with MUSC Health’s first total talus replacement.
“We only have about 18 months of data on this procedure overall. But I think it’s important to have this option. We’re able to offer it with full informed consent, having a thoughtful conversation with patients and doing what’s right for them,” says Gross.
The procedure, which happened in August, was the first time a 3D-printed orthopedic prosthesis had been used at the institution. (Currently, MUSC Health does not create commercial prostheses for this procedure; the talus prosthesis was created by Additive Orthopaedics, based in Little Silver, New Jersey).
Part of the reason talar replacement is even possible is because the talus is an inherently stable bone. “The talus is hard to pop out, even though muscles and tendons aren’t attached to it,” explains Gross. “It uses force of weight to stay in place, so it’s a natural for replacement.”
Contraindications for total talus replacement are minimal: those who have an active infection or arthritis in the surrounding joints.
Making it happen
To start the process, the patient’s healthy leg and foot are imaged by CT scan; then the image is flipped and becomes the model for the new talus. Three models are 3D-printed: one that’s an exact duplicate, and two more, each with 1 millimeter of variation in either direction to account for variability. This particular prosthesis is made of cobalt chromium, but others may also be made from titanium and cobalt.
During the procedure, the patient received a nerve block, which put her under twilight anesthesia. An incision was made at the front of the ankle, in the interval between the tibial and extensor hallucis longus tendons to expose the articulation between the talus and tibia. Soft tissue attached to the talus was dissected, and the talus was removed in four pieces. Once removed, models of the prosthesis were inserted to determine ankle stability and range of motion. After that was established, the actual prosthesis was put in place. The entire procedure took about 45 minutes, says Gross.
Faster recovery and improved quality of life
One of the exciting features of talar replacement is its faster recovery time. “When you have femoral head allograft surgery, it’s difficult to make sure the new bone receives enough blood flow,” Gross explains. “The patient needs to spend about 12-16 weeks off their feet. But with a 3D-printed talus, they’re walking in two weeks.”
As for August’s patient, Gross says she’s doing great, although data on the procedure is still limited. “While fusion is the gold standard for most foot and ankle procedures, people value range of motion. Eventually it’s going to get easier and easier and less and less expensive to 3D-print prostheses,” explains Gross.
“It’s an interesting intersection of technology and medicine,” he says. “We don’t know what the future holds, but we do know this is promising.”
Source: Progressnotes Fall 2018